Yes, I know. I should have given an update about my first encounter with Metal Adventures’ Copprclay two weeks ago, but between getting ready for my first ever fair – CRAFTfest and taking care of a baby, there is little or no time at all to do anything else. And of course, the Olympics, how can I forget that?
First of all, congratulations to Team GB, they did marvelous right up to the end. They really did us all proud. And to the other countries who participated. There were many memorable moments for me, but the one I will never forget was the encouragement spectators gave a female athlete from Saudi Arabia I think, who though came last in one of the races, but who finished the race with a resounding applause from the spectators.
Okay, back to the topic of the day. I opened my kiln the next morning, took out the pieces and found them looking okay (no obvious sign of under/over-firing) and with some kiln patina in places. But having had almost a year’s experience with firing FASTfire Bronzclay (let me say here that a good number of those firings brought tears to my eyes), I knew that seeing is not always believing. So, I checked to see that every piece fired well by first trying to bend my test piece. The piece was about 3.5mm thick, it bent to 180 degrees with some sweat. I had to employ the services of MDH to bend it, and it wouldn’t go beyond 180 degrees as it was too short, first test passed. I measured with my eyeometer, and saw that they all shrank about 20% (see pictures). 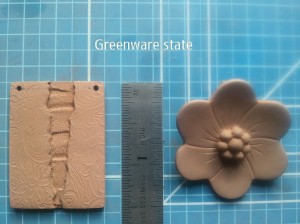
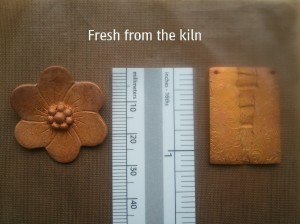
So I felt more confident. Then, I threw my real pieces on my kitchen floor to see if they’ll break, but they didn’t, and that confirmed to me that they fully sintered. I then steel-brushed them and the well-known pinkish colour associated with copper presented itself.
Though not bad-looking with their natural colour, I decided to patina them instead, and that also gave me some hassles. I first tried the much acclaimed heat patina I’d heard so much about on a pair of earrings, but I didn’t get similar colours on each. So, I decided to use liver of sulphur (LOS). Unlike fine silver, it’s not possible to remove patina from copper with flame, so I just forged ahead. I then found that it reacted very quickly with LOS, and I found it almost difficult to control. It even seemed to me that it kept on reacting to the LOS even after neutralising with baking soda.
Lest I forget, I found it very messy to work with and calling it dirty will not be far from right, but it doesn’t dry as fast as fine silver metal clay, so, you have a longer working time with it. All in all, I’m very happy with my first attempt, so much so that I’m currently working on mixing it with FASTfire Bronzclay in a bangle. I’ve decided to add only a little copper to this bangle as it sinters at a much higher temp (954 degrees celsius) than FASTfire Bronzclay (810 degrees celsius). Firing a piece that combines the two will have to be done at the lower temperature lest the bronze overfires.
Here are the finished pieces, after patinating and given a protective coating.
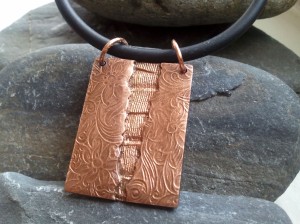
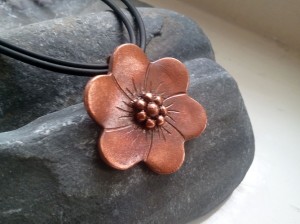